Enhancing EBARA's Casting Quality Globally
Developing Young Employees Through Training
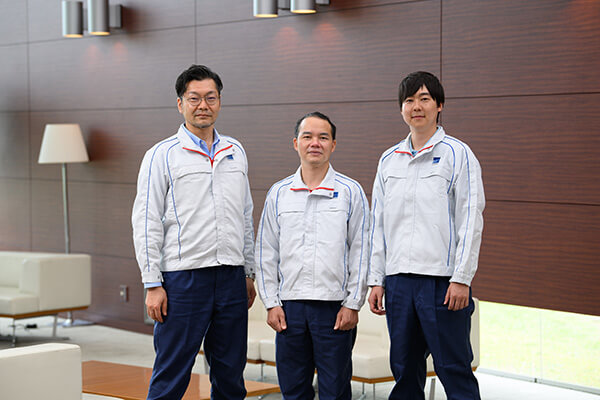
Monozukuri (manufacturing) by learning and improving both digital and on-site aspects with trainees from Vietnam
As part of its globalization efforts, the EBARA Group has implemented a unique training program called the Global Career Development Program (GCDP). Young employees from the EBARA Group all over the world undergo training for two years in various parts of the world, including Japan. Do Van Nghiem, who came to Japan in 2023 from Ebara Vietnam Pump Company Limited (EVPC), is one such trainee.
Training is provided at the Ebara Manufacturing Technology Advanced Center (EMTAC), a “monozukuri” (manufacturing) base for the entire EBARA Group.
The Itabashi and Narita teams at EMTAC that accepted the trainees created their own system using a radar chart to show the trainees' level of growth over the two-year period. We asked Takayuki Narita, Yosuke Itabashi, and Nghiem, three members of the Prototype & Manufacturing Collaboration Section in the Manufacturing Technology Development Department at the Innovative Production Engineering and Quality Assurance Division to share their thoughts on casting.
Value in sharing knowledge about casting around the world
——Nghiem, why did you want to do your training in Japan?
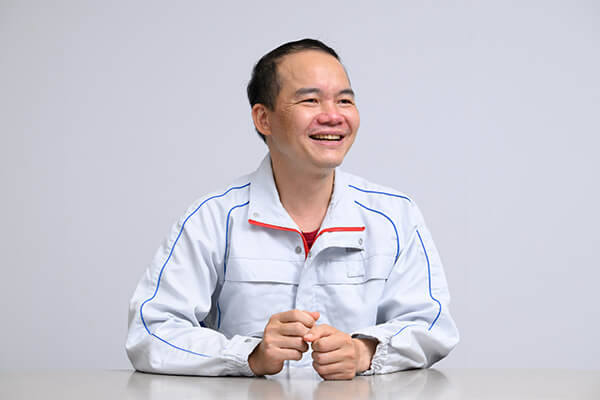
Ebara Vietnam Pump Company Limited
Nghiem—I am responsible for inspections at EVPC in Vietnam. This means I check the quality, defects, and scratches and measure dimensions of finished castings (*products made by pouring molten metal at high temperature into a mold and cooling them to harden.) I came to Japan because I wanted to improve these skills. For this training, I was assigned to Narita and Itabashi's teams.
Narita: Our division is engaged in the rapid prototyping of development prototypes required by various divisions, and also works with bases to help resolve issues in the field. There are several teams within the division. Nghiem and Itabashi are on the casting team. Casting is a process for making castings in which metal is melted, poured into a mold, and then allowed to harden. Itabashi is involved in the 3D measurement of the finished castings.
Itabashi—Casting involves numerous processes. Small differences in each process have a large impact on the final product. For example, even if the same mold is used, slight changes in conditions and environments at any given time can cause differences in the finished outcome.* So, we measure the dimensions of the casting and see if there are any errors between the post-machining shape and the designed shape. Up until now, specialists did this measuring manually. By using a special machine to perform the 3D measurement, we ensure that the inspection results do not depend on the ability of workers. Doing so also significantly reduces inspection times.
Narita—At EMTAC, we aim to deliver prototypes required by various departments within three days. Shortening measurement times is a necessary skill to make prototypes quickly.
Itabashi—EVPC in Vietnam also has 3D measurement equipment, so I would like to see Nghiem learn how to perform 3D measurements and all other methods of inspecting and evaluating castings, and pass them on to other workers in Vietnam.
——What do you think is the significance of having young employees cross borders and share expertise through such training?
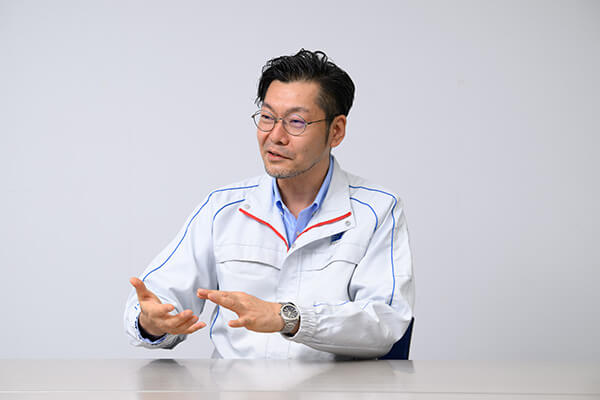
Prototype & Manufacturing Collaboration Section, Manufacturing Technology Development Department, Innovative Production Engineering and Quality Assurance Division
Narita—Up until now, EBARA employees in Japan received training at overseas group companies. But in 2022, GCDP was started as a two-way training program that sends EBARA employees from all over the world to other countries, including Japan. We want to send out more young employees who desire the training, and by accepting trainees, we can create global friendships. It is very significant that people with similar aspirations can be found at each base.
In particular, because there are many factors that affect the original quality* of castings and many items that must be managed, there are likely many bases around the world that are struggling with issues and concerns. As we mentioned earlier, even if the same mold is used and the metal is poured in the same way, there will be slight variations in the finished product. In addition, bases that manufacture many one-of-a-kind products or small quantities of many different products require detailed adjustments each time. Given this, I think it is important that we have more colleagues like Nghiem and that we can share issues and solutions with each other around the world.
In addition, we would like to encourage the use of 3D data beyond 3D measurement at all bases. We want to see it used to consider design and manufacturing methods in advance to prevent defects. In addition to the manufacturing process and measurement after manufacturing, it can be used for simulations and analysis before manufacturing. We therefore aim to increase the number of colleagues and have 3D data used effectively at bases around the world.
For castings at the EBARA Group, the quality that is determined during the processes of molding, covering, melting, and casting is called "original quality." This is different from quality that meets specifications. We strive to improve this original quality and keep in mind how we can eliminate subsequent additional processes (such as repairs).
Creating radar charts to visualize growth over the two-year period
——Was there anything done differently in Nghiem’s training?
Narita—We created a radar chart to help visualize Nghiem's level of growth during the training period. A radar chart has multiple axes, each representing a different variable; the data points are plotted along their axis to form a polygon. It is similar to a spider chart, often used for analyzing a team's strength. For example, we broke down “inspection” as a skill into five levels. Itabashi and I then discussed the requirements of each level, like what does Level 2 mean and how is it different from Level 3 and so on.
We want Nghiem to acquire the knowledge and skills needed to be an inspector, including 3D measurement, over the two-year period. Our hope is that he will be able to inspect castings to the point where he can not only find defects but also predict the cause and the process in need of improvement based on the condition of the defect. It may be requesting too much, but we created a radar chart with that much in mind. We measured Nghiem's technical level at the time of his arrival in Japan, and then we considered what level we want him to reach in two years' time and the curriculum necessary to achieve that.
However, although I have a long career in casting, I am not an inspection or measurement specialist. Itabashi is also familiar with 3D measurement, but there are many things that we do not know about inspections performed manually. Given this, it was difficult to assign inspector skill levels to the radar chart. Itabashi was a huge help.
Itabashi—Regarding the manual inspections and measurements, I talked to employees who currently perform inspections. There are also areas of the curriculum that our team is unable to teach on its own. Therefore, we asked Nghiem to learn about inspection technologies at the EBARA Futtsu Plant for about two months.
Nghiem—I learned a lot from everyone at the Futtsu Plant. I was nervous, but it was a valuable experience to be able to see the inspection process in Japan and the performance tests carried out after a product is completed up close.
Narita—I think this radar chart can be applied in the future when other trainees are accepted through GCDP or when providing technical guidance to new employees.
——Itabashi, what did you keep in mind when teaching skills and expertise to Nghiem?
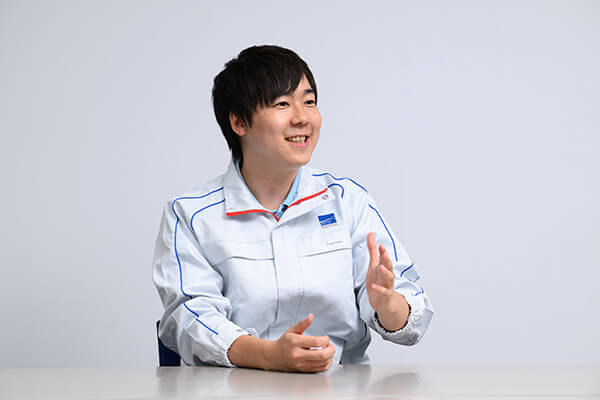
Casting Team, Prototype & Manufacturing Collaboration Section, Manufacturing Technology Development Department, Innovative Production Engineering and Quality Assurance Division
Itabashi—I assumed I would not be able to teach Nghiem unless I understood the subject well myself, so I studied hard using documents and so on. And in order to deepen his understanding of casting, we were able to provide a hands-on experience to help him get a feel of the actual casting process.
Gaining a deeper understanding of the process will help Nghiem become able to find defects during inspections, identify which step in which process is causing the problem, and what improvements need to be made. That is why we came up with this curriculum.
Nghiem—I now understand the process of making castings and that there are many different steps involved. I am also glad to have gained a broad understanding of the different types of defects. My task now is to remember them and apply this knowledge during inspections.
An opportunity for the host division to also learn about casting
——Was there anything the two of you from EMTAC gained through Nghiem’s training?
Itabashi—I was able to supplement areas where I lacked knowledge, such as manual inspections and the casting process. I feel that I learned a lot from teaching Nghiem and creating the radar chart for the training.
Narita—With this training, I wanted Nghiem to grow. But I also wanted Itabashi to gain from this opportunity. I feel like we are achieving that.
Today, we use data, technology and advanced simulations to create products more and more. 3D measurement is one such example of this, and Itabashi has gained knowledge about 3D measurement and the related data. However, I do not want trainees to become people who cannot work without data or technology. Not understanding the knowledge and skills being used on-site and only being able to understand the digital side of things leads to a disconnect from manufacturing sites.
I want people to learn the technologies after learning the processes and principles of a site; I want them to acquire both. I am sure the GCDP also gave Itabashi an opportunity to learn both.
——What are your goals for the future?
Nghiem—During my time in Japan, I hope to learn about 3D measurement and inspections, and then share this knowledge with others at my plant in Vietnam. Even after I return to Vietnam, if there is anything I do not understand, I hope to consult with everyone here in Japan.
Narita—Good idea. I think that Nghiem bringing the skills with him back to Vietnam will lead to improvements in inspection quality in Vietnam. Personally, I hope to contribute to lifting up the entire EBARA Group as a whole by engaging in human resource development through GCDP and other opportunities. In today’s world, doing the obvious is no longer enough. It is important to make further efforts to produce good products while also reducing our impact on the environment. The same is true all over the world, so I would like to share our knowledge with those at various bases and work together.
Itabashi—I want Nghiem to make use of what he learns here in Vietnam, and I will make sure that we always work together. As for my own goals, I want to continue learning about casting techniques. In particular, I want to acquire on-site knowledge similar to what I experienced this time around. Casting truly is difficult, and the results vary widely depending on just small changes in the conditions. That’s why I want to be on site and learn more.
Narita—Casting is certainly difficult. That's why I hope that young workers, including Itabashi, will work hard to learn how to get better without giving up because it is difficult. I want to create that kind of team.
The EBARA Group is expanding globally
Introducing the Ebara Vietnam Pump Company Limited (EVPC)
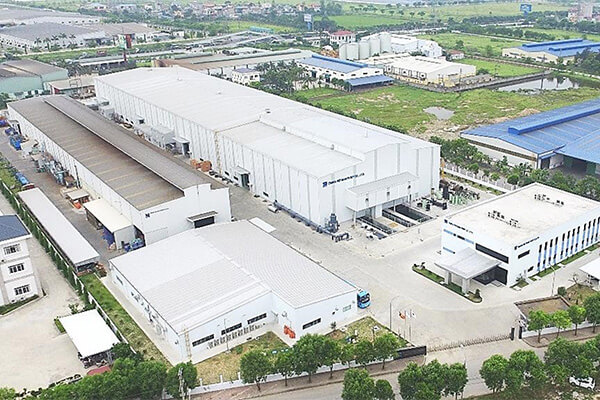
Ebara Vietnam Pump Company Limited(EVPC)
Ebara Vietnam Pump Company Limited (EVPC) was established in 1995 as EBARA Hải Dương (EHD) in Hải Dương Province, Vietnam, as a joint venture between EBARA Corporation and a pump manufacturer in Vietnam. It became a wholly-owned subsidiary of EBARA Corporation in 2011, changed its name to EVPC, and completed a new plant in 2016.
The plant has manufacturing capabilities for raw materials (castings and fabrication), and is the only pump plant in the EBARA Group that can provide integrated production from raw material manufacturing to machining, assembly, and testing.
In particular, it is difficult to accurately reproduce the design shape for castings. For impeller castings, which affect pump performance, 3D scanning technology is used to verify deformation and inspect shapes during the manufacturing process. In addition, the plant aims to manufacture defect-free castings by identifying the causes of casting defects and preventing their recurrence, as well as by considering casting design and making full use of analytical software.