掲載号: No. 256〔講座〕
「腐食防食講座−高温腐食の基礎と対策技術−」
第6報:高温機器における浸炭,窒化及び水蒸気酸化事例と対策
Lecture on Fundamental Aspects of High Temperature Corrosion and Corrosion Protection
Part 6: Examples of Carburization, Nitridation and Steam Oxidation in High-temperature Devices and Countermeasures
執筆者
八鍬 浩*
Hiroshi YAKUWA
野口 学**
Manabu NOGUCHI
- *
技術・研究開発統括部 基盤技術研究部
- **
技術・研究開発統括部 製品コア技術研究部
本報では,環境・エネルギー関連装置で見られる浸炭,窒化及び水蒸気酸化の事例と対策について紹介した。浸炭は炭化水素や一酸化炭素を含む環境で見られ,合金中のクロムと炭化物を形成することで合金の耐食性を低下させる。窒化はアンモニアを含んだ環境で生じ,腐食による減肉よりも,材料を脆化させて機械的特性が損なわれることが問題となる。水蒸気酸化は,水素の共存によって,大気中での酸化と比較して酸化速度が著しく大きくなるのが特徴である。いずれも,表面に保護性の高い酸化物皮膜を形成するための合金選定/合金設計が,腐食を低減する上で重要である。
This section focuses on carburization, nitridation, and steam oxidation, which are found in equipment relating to environments and/or energy, and relevant corrosion protection. Carburization, which is found in environments containing hydrocarbons, degrades the corrosion resistance of alloys by combining carbides with the chromium in the alloys. Nitridation, which occurs in environments containing ammonia, causes materials to become embrittle resulting in impaired mechanical characteristics. This problem is more serious than thickness reduction due to corrosion. In the case of steam oxidation, the oxidation rate in the presence of hydrogen is much higher than that in the air. Selection and design of alloys that form protective films on alloy surfaces is important for the reduction of corrosion in the above cases.
Keywords: High temperature corrosion, Carburization, Metal dusting, Steam oxidation, Nitridation, Ammonia, Reducing atmosphere, Protective film, Hydrocarbon, Water vapor
1.はじめに
環境・エネルギー関連装置においては,プロセスによって様々な環境条件(温度域やガス組成など)に装置材料がさらされることになる。化石燃料の主成分である炭化水素系のガスやCOあるいはCO2を含んだガス中では,浸炭やメタルダスティングを起こすことがある。また,アンモニアを含む環境や,1000 ℃を超えるような高温では窒素によって窒化が生じることもある。浸炭や窒化では,酸化や硫化と異なり,表面での腐食スケール形成が支配的な腐食損傷形態ではなく,合金内部で変質層を形成して耐酸化性を低下させたり,あるいは材料の機械的特性を損なったりする腐食損傷形態をとることが多い。
本講座の第1報から第5報において,高温腐食と防食の基礎,廃棄物処理関連設備における塩化腐食及び石油精製関連機器における硫化腐食について詳しく述べた。本報では,その他の環境・エネルギー機器に特徴的な高温腐食形態として,浸炭/メタルダスティング,窒化及び水蒸気酸化の事例について概説する。
2.燃焼器における浸炭/メタルダスティング事例と対策
2-1 浸炭/メタルダスティングが起こる環境
浸炭は,ガス相中の炭素活量と合金中の炭素活量の差,すなわち

の条件下で生じる。ガス中の炭素活量は,式(6-2)~式(6-4)の平衡定数によって決まり,各温度に対する値は図6-1 1)のようになる。すなわち,約600 ℃を境に低温側ではCOを含んだガスで浸炭性が高くなり,高温側ではCH4(炭化水素)を含んだガスの浸炭性が高くなることが分かる。一方,合金中の炭素活量は,例えば炭素鋼であれば,式(6-5)の平衡定数から計算することができる。
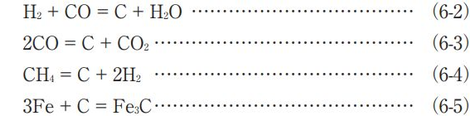
しかしながら,実用合金では,FeとC以外にも種々の元素が添加されている。添加元素は合金中の炭素活量a
cを変化させる。SiやNiは鋼中の炭素活量を上げ,V,Cr,Moなどは炭素活量を下げる 2)。すなわち,SiやNi含有量の多い鋼は浸炭しにくく,V,Cr,Mo含有量の多い鋼は浸炭されやすいことになる。
メタルダスティングは,浸炭の一種で,グラファイトが析出しないと仮定した場合の合金表面での炭素活量が,計算上1を超えるような高炭素活量環境で生じ,グラファイトの析出と金属の紛化を伴って異常減肉をもたらす現象である。メタルダスティングは,炭素鋼及び低合金鋼では以下のようなメカニズムで生じるといわれている 3),4)。すなわち,雰囲気の炭素活量が高い場合,Cが材料中に固溶してセメンタイトを析出する。次いでグラファイトが析出することによってセメンタイトはFeとCに分解する。一方,オーステナイト系ステンレス鋼やNi基耐食合金では,孔食状の減肉形態をとることが多い。これらの合金では,合金表面の保護性酸化物皮膜の欠陥部を通して浸入したCによって炭化物(M23C6,M7C3)を形成する。更に合金素地が過飽和状態となって,直接グラファイトの析出を引き起こす 5)~7)。メタルダスティングは,水素製造や合成ガス製造プロセスで顕在化し,特にCOガスを含んだ環境において,400~800 ℃の温度域でみられることが多い 5)~7)。

図6-1 炭素活量に関わる反応の平衡定数 1)
2-2 浸炭に起因する燃料混合管の高温腐食損傷
図6-2 8)に,空気と燃料を混合しながら燃焼器に燃料を導入する燃料混合管(Co-28%Cr-20%Fe合金製(mass%))に発生した浸炭に起因する損傷事例を示す。これは,燃焼器として約2400時間運転された燃料混合管の断面である。燃料混合管の内側は燃料であるプロパンガスがリッチな還元性雰囲気になり,管外側は燃焼ガスとなるため酸化性雰囲気となる。管壁表面の温度は正確には把握できていないが,管内側は1000 ℃未満,管外側であっても1000 ℃前後ではないかと推定された。この管は,最も厚い所で3 mm以上の肉厚があるが,管の肉厚方向全体が腐食損傷を受けていた2400時間で肉厚3 mmの管全体が腐食すると仮定すると,腐食速度は10 mm/y以上となる。これは,1093 ℃の大気中におけるCo-27%Cr-18%Fe合金の熱サイクル酸化速度 9)よりも著しく大きい値であることから,単純な酸化によって損傷したとは考えにくい。図6-2(a)8)に示したように,管内壁面近傍では,合金内部に多量のCrリッチな炭化物が析出しており,合金基材のCr濃度は約10 mass%にまで低下していた。それに対し,外壁面から数百μm内部(図6-2(b))8)では,炭化物と基材の界面に沿って粒を取り囲むように内部酸化が進んでおり,酸化が合金内部に及んでいる様子が伺える。さらに,管外壁面近傍(図6-2(c))8)では厚い酸化物が成長していた。以上の観察結果から,燃料混合管の損傷機構を図6-3のように推察した。管内壁側は燃料リッチな還元性ガス雰囲気であるため,燃料から解離したCによって浸炭が生じる。浸炭は基材内部へ進行し,外壁表面にまで達する。一方,外壁側は酸化性の燃焼ガス雰囲気であるため高温酸化が進行する。その際,炭化物が析出した基材はCr濃度の低下によって耐酸化性が低下しているのに加え,炭化物と基材の界面に沿った内部酸化によって合金内部に深く酸化が進行し,激しい腐食損傷を生じたものと考えられる。
以上より,本混合管の異常減肉は,健全な組成を有する合金素地の高温酸化ではなく,浸炭による炭化物形成によって有効Cr濃度が低下したことに加え,炭化物が腐食性ガスの優先拡散経路を提供したことに起因すると考えられる。そのため,本環境での耐食性を向上させるには,材料の耐浸炭性を向上させる必要があると判断した。材料の耐浸炭性を向上させるには,合金表面に保護性の高い酸化物を連続層として形成し,炭素の合金表面への到達を抑制すること,及び合金中の炭素の拡散速度が小さい組成の合金を選定することが有効と考えられる。高温下において保護性の高い酸化物は,Cr2O3及びAl2O3である。Al2O3はCr2O3と比較して酸化物成長速度係数が約2桁小さい 10)ため,より有効な保護成皮膜になると考えられるが,剥離しやすい欠点を有するため,剥離防止対策の併用が必要となる。一方,Cr2O3は,幅広い温度域で良好な耐食性を示し,ほとんどの一般産業機械用耐熱用材料として広く利用されていることから,保護性酸化物皮膜としてCr2O3を利用することが好適と考えられる。
合金表面に継続的にCr2O3の連続皮膜を形成するには,Cr2O3の外部酸化皮膜形成に必要なCr濃度が少ない合金系が有利である。Ni-Cr系は,Co-Cr系と比較してCr2O3外部酸化皮膜形成に必要なCr濃度が少なくてすむため 11),継続的にCr2O3の連続皮膜を形成するのに有利である。さらに,Fe-Ni-Cr系合金において,Ni含有量が増えると耐浸炭性が向上する 12)ことから,浸炭を低減するには,Ni-Cr系合金が有利と考えられる。以上より,管材料をCo-Cr系合金からNi-Cr系合金に変更することで,寿命延伸を可能とした。

図6-2 燃料混合管に発生した浸炭に起因する損傷箇所の断面と特性X線像 8)

図6-3 予想される燃料混合管損傷プロセスの模式図
2-3 燃焼器内壁に発生したメタルダスティング事例と対策
図6-4 8)は,2-2節で紹介した高温腐食損傷を生じた燃焼器と同じ型の燃焼器の内壁に生じた食孔状の腐食である。燃料や運転温度は2-2節で紹介したものとは異なり,雰囲気にはCOを含み,ガス温度はやや低めで800~900 ℃と推定された。燃焼器の材料は,耐熱材料として種々の高温装置に実績のあるNi-Cr-Mo-Fe合金である。図6-4のA-A断面を図6-5に示す。食孔はきれいな半球状で,径の中心付近において最も減肉が深かったことから,食孔中心部から等方的に成長したことが伺える。食孔の淵の部分図6-5(a)と食孔底部付近の図6-5(b)の合金表面付近及びスケールの元素マップを図6-6と図6-7にそれぞれ示す。食孔の淵の元素マップ(図6-6)から分かるように,食孔の外は合金表面が厚さ5μm程度のCrリッチな酸化物と,ガス中に含まれるSi系成分に由来すると思われるSiリッチな酸化物層で覆われていた。それに対し,その極近傍であっても,また,最も減肉の激しい食孔底部付近(図6-7)であっても,食孔内は合金表面の酸化物皮膜が非常に薄いか,あるいは存在していなかった。さらに,図6-7に示したように,食孔内部においては,表面にCの析出が見られた。

図6-4 燃焼器内壁に発生した食孔状の腐食 8)

図6-5 燃焼器内壁に発生した食孔状の腐食の断面
(図6-4のA-A断面)8)

図6-6 図6-5(a)の箇所の特性X線像

図6-7 図6-5(b)の箇所の特性X線像 8)
図6-8 8)に,食孔内外の合金内部から内壁面合金表面に向かって板厚方向にとったCのプロファイルを示す。Line1と2が食孔外部におけるプロファイルで,Line3~5が食孔内部におけるプロファイルである。合金内に所々見られるスパイク状のピークは炭化物と思われる。食孔外部であるLine1及び2では,合金内部と内壁面合金表面近傍において,Cの特性X線強度に大きな差異は見られない。このことは,合金表面が健全な酸化物皮膜で覆われていれば,合金中へのCの侵入が抑制されることを示している。一方,食孔内部であるLine3~5では,いずれも合金表面から0.09~0.1 mmの深さまでのCの特性X線強度が大きくなっていることが分かる。特徴的なことは,Cの侵入深さが食孔内のいずれの場所でもほぼ同じことである。今回の減肉が食孔状に成長していること,食孔内の内壁面合金表面から一定の深さにおいてC濃度が増加していること,及び食孔内の合金表面にはCが析出していたことなどを考え併せると,本食孔は,表面酸化物皮膜の欠陥部を起点として発生した,いわゆるメタルダスティングであると考えられる。

図6-8 燃焼器内壁に発生した食孔状の
腐食部近傍のCプロファイル 8)
以上より,燃焼器内壁に食孔を生じる過程を模式的に図6-9 8)に推察する。すなわち,内壁面表面に生成した酸化物皮膜の欠陥を通して雰囲気中のCが侵入する。Cが合金中に過飽和状態になると,グラファイトを析出するとともに,基材金属が紛化する。Cの侵入は,酸化物皮膜の欠陥部から成長するため,減肉は食孔状になるものと考えられる。したがって,2-2節で示した混合管にみられた浸炭の対策と同様に,合金表面に保護性の高い酸化物を連続層として形成すること,及び合金中の炭素の拡散能が小さい組成の合金を選定することが有効な対策と考えられる。混合管には,Co-Cr系合金を使用していたため,より連続Cr2O3皮膜を形成しやすく,かつCの拡散能が小さいNi-Cr系合金へと材料を変更することで寿命延伸を達成した。一方,本燃焼器には既にNi-Cr-Fe-Mo系合金を使用していることから,更に予備酸化処理を施し,強固で保護性の高いCr2O3皮膜をあらかじめ形成させることによって,長寿命化を図る対策を講じた。
なお,2-2節で示した混合管の浸炭対策でも同様に考察したが,Cr2O3よりも安定な酸化物であるAl2O3を形成するような対策も有効と考えられる。例えば,Al2O3フォーマーのNi基超合金を用いる方法も考えられるが,コスト面からはアルミ拡散処理等で表面にアルミ濃化層を形成する方法も有効と考えられる。それらの場合,Al2O3皮膜の剥離を防止する対策を併用することが望ましい。

図6-9 推定されるメタルダスティングによる
食孔形成プロセス 8)
3.アンモニア/水混合雰囲気における鉄鋼材料の高温腐食挙動
鉄鋼材料が水蒸気を含む高温環境にさらされると,水蒸気酸化を生じることが知られている 13)。ステンレス鋼製ボイラ管の場合,水蒸気酸化によって表面スケールが厚く生成すると,ボイラの冷却時にそのスケールが剥離してボイラ管内に堆積し,蒸気流路を閉塞する。その結果,ボイラ再起動時に管が過熱されてクリープ損傷を起こす事故が報告された 14)。現在では,材料面(細粒材使用, 冷間加工材使用など)及び運転・保全面(管温度上昇防止, Uベンド部の検査など)の両面から対策が講じられている。
一方,アンモニアによる窒化腐食事例は,アンモニア合成プラントにおいて報告 15),16)されている。NH3ガスが合金表面に吸着して分解し,原子状Nが合金内部に拡散して固溶体や窒化物を形成することによって機械的特性を損なったり,あるいはステンレス鋼などのCr含有合金では,Cr窒化物形成によってCr欠乏層を生成して耐食性低下の原因となったりすることがある。鉄鋼材料は,材料にもよるが,約450~700 ℃のアンモニア中で窒化して,特に靭性が損なわれる。炭素鋼においては,200 ℃と比較的低い温度域においても脆化することが報告されている 17)。
アンモニア/水蒸気混合ガス系においては,水蒸気酸化と窒化の両方が懸念されるが,アンモニア/水蒸気混合ガス系における金属材料の腐食挙動については詳しい報告がなく,不明な点が多い。そこで,本章では,アンモニア/水混合ガス中における各種合金材料の高温腐食挙動を実験によって調べた結果 18)について述べる。
3-1 アンモニア/水蒸気混合ガス中への鉄鋼材料の暴露試験
実験は,400 ℃,500 ℃あるいは565 ℃に保った反応装置に,NH3:H2O=8:2の混合液を一定速度で供給して,低合金鋼(1Cr鋼)とステンレス鋼(12Cr鋼)を暴露することで行った。この際のアンモニアの分解量は約5 %であった。暴露後,試験片を反応装置から取り出して常温引張試験に供し,機械的特性に及ぼすアンモニア/水蒸気混合ガス中に対する暴露の影響を調べた。
図6-10に,565 ℃で1000時間アンモニア/水蒸気混合ガス中へ暴露した後,常温引張試験に供した12Cr鋼の破面及び断面を示す。破面には,表面から約350μmの平坦な脆性破面層が見られた。一方,断面には表面に約50μm程度の黒色の酸化層とその下に素地とは色の異なる窒化層が約300μm見られ,更にこれらの層を貫いてクラックが発生していた。破面観察で表面から脆性破面層が見られたこと,及びクラックがこれらの層を貫いて発生していることから,これらの酸化層及び窒化層は脆く,厚く生成することで材料の耐衝撃性を低下させることが示唆される。
図6-11に,1Cr鋼と12Cr鋼のアンモニア/水蒸気混合ガス中への暴露有無による常温引張特性の差異を示す。1Cr鋼は,500 ℃以下の暴露で脆化層はほとんど生成せず,暴露前後による機械的特性の変化は小さかった。したがって,1Cr鋼にとって,500 ℃以下/500時間のアンモニア/水蒸気混合ガス中への暴露は,機械的特性に大きな影響を及ぼさないものと考えられる。しかしながら,本環境中での構造材料としての適用可否を判断するには,より長時間の暴露試験が必要である。一方,12Cr鋼は,500 ℃の暴露によって,引張強さ及び耐力に大きな変化は見られなかったが,伸び及び絞り(延性)の低下が見られた。これは,Cr濃度が高いため,500 ℃であっても数十μmの窒化層を形成し,延性低下に寄与したためと考えられる。565 ℃の暴露によっても,引張強さ及び耐力に大きな変化は見られなかったが,延性が著しく低下した。これは,図6-10に示したとおり,表面から約350μmに及ぶ厚い脆化層を形成したことに起因すると考えられる。
アンモニア:水蒸気=8:2の混合ガス中への鉄鋼材料の暴露によって,表面には,酸化スケールを形成し,その直下の合金内部に窒化層を形成することが分かった。酸化スケールと比較して窒化層は厚く成長するが,窒化層が厚く成長しても引張強度と耐力の低下度は小さかった。しかしながら,材料の延性(伸び,絞り)は,窒化層が厚くなるにつれて低下した。400 ℃では脆化層の成長速度は小さく,数百時間の暴露では延性低下の度合いが小さいが,500 ℃以上,特に565 ℃では脆化層の成長速度が大きいため,延性が著しく低下することが分かった。本環境において材料特性を低下させているのは,酸化層と比較してより厚く形成する窒化層が主原因と考えられるが,アンモニア/水蒸気混合比,温度及び材料組成によっては異なる挙動を示すことも考えられるため,環境に合わせた材料選定,材料設計が必要となる。おそらく,表面酸化物層の保護性の高さと窒化のしやすさが材料特性を支配するものと推察される。特に使用温度が高い場合,高温強度及び耐酸化性の観点から,Cr含有合金あるいはステンレス鋼が使われることが多い。Crは,保護性酸化皮膜形成元素であるが,一方で窒化物形成元素でもあるため,合金中のCr濃度が低く保護性酸化皮膜を安定に形成できない場合,Nが合金中に侵入して合金内部でCr窒化物を析出することで,かえって材料の脆化を助長する。一方,Cr濃度が高く保護性酸化皮膜を安定に形成できる場合は,合金中へのN侵入が抑制され合金内部でのCr窒化物析出が生じないため,正常な材料特性を維持できるものと考えられる。したがって,Cr含有合金をアンモニア/水蒸気混合雰囲気で使用する場合は,当該環境において保護性酸化皮膜を形成するのに十分なCr濃度を有した材料を使用する必要がある。

図6-10 565℃で1000hアンモニア/水蒸気混合ガス中へ暴露した後,
常温引張試験に供した12Cr鋼の破面及び断面

図6-11 1Cr及び12Cr鋼の常温引張特性に及ぼすアンモニア/水蒸気混合ガス中への暴露の影響
(暴露時間:500h,ただし,400℃に暴露した12Cr鋼は1000h)
4.ステンレス鋼の水蒸気酸化挙動
3章で述べたとおり,ステンレス鋼などの鉄鋼材料が水蒸気を含む高温環境にさらされると水蒸気酸化を生じる。一般に,水蒸気中では,酸素や大気中と比較して酸素ポテンシャルが低いにもかかわらず酸化速度が大きく 19),また,酸化速度が単純な放物線則に従わないことや,一定の誘導時間を経たあと酸化速度が著しく大きくなる加速酸化を起こすこともある 20)。そのため,大気あるいは酸素による酸化と比較して,構造部材の損傷要因となるリスクが高い。しかしながら,環境・エネルギー関連装置では,燃焼ガスを取り扱うことが多々あり,装置部材は少なからず水蒸気含有環境にさらされることになる。したがって,装置部材の水蒸気酸化挙動を把握して,適切な防食対策を講じることは,環境・エネルギー関連装置にとって重要である。
Fe基合金の水蒸気酸化においては,多数のボイドを含んだ厚いスケールが形成されることが知られている。水蒸気酸化が,大気あるいは酸素中の酸化と比較して速度が著しく大きくなることの説明として,スケールのボイド中を水蒸気として酸素が移動することによって内層スケールを厚く成長させるという機構がFujiiら 21),22)及びRahmelら 23)によって提案されている。さらに,様々な研究者 24),25)によって,酸化に及ぼす水蒸気や水素の影響について検討されており,これらがボイド内に存在して酸化挙動に影響を与えることが示されている。
高温装置部材にステンレス鋼が使用される場合,高温強度の観点から,オーステナイト系ステンレス鋼が使われる場合が多い。そこで本章では,高温装置部材として汎用的に使用されるSUS304鋼及びSUS310S鋼について,水蒸気含有環境における基本的な酸化挙動を調べるために行った酸化実験結果を紹介する。
4-1 水蒸気酸化挙動に及ぼす熱サイクルと酸素分圧の影響
高温装置部材に水蒸気酸化が生じると,厚く成長したスケールが剥離し,装置の閉塞や後段の装置のエロージョン要因になる可能性がある。酸化スケールは,合金素地と比較して熱膨張係数が小さいため,冷却時に剥離する可能性がある。そこで,図6-12のように,熱天秤で試験片の重量を測定しながら電気炉を昇降できる実験装置を製作し,水蒸気酸化スケールの剥離挙動を調べた。昇温時から,800 ℃で14時間保持,その後電気炉を下げ試験片近傍のガス温度が250 ℃になった時点までを1サイクルとし,このサイクルを10回繰り返すことで試験片に熱サイクルを付与した(図6-13)。酸化挙動に及ぼす酸素分圧の影響を調べるため,実験ガスとして表6-1に示す4通りを用いた。すなわち,所定の水蒸気分圧になるよう恒温槽で水温調整した純水の飽和蒸気圧を含むように,N2,N2-H2あるいはN2-O2混合ガスをキャリアガスとして水蒸気を反応槽に導入した。
図6-14に,大気中及び水蒸気含有環境に暴露したSUS304鋼の断面写真を示す。大気中では,部分的にノジュール状の腐食が見られたが,表面のほとんどは数μmの薄い酸化物で覆われており,皮膜の剥離も見られなかった。一方,水蒸気含有環境に暴露したSUS304鋼は,皮膜は厚く成長し,皮膜が剥離した形跡が見られた。酸素分圧の低いガス(a)(N2-3.4%H2-15.5%H2O(PO2=9.3×10-18atm))に暴露したSUS304鋼は,内層スケールと外層スケールの界面から剥離が生じている様子が分かる。一方,酸素分圧の高いガス(d)(N2-16.9%O2-15.5%H2O(PO2=1.7×10-1atm))においては,外層スケールはほとんど残存しておらず,かつ内層スケール内部からも剥離が生じている様子が見られた。
図6-15に,水蒸気含有環境であるガス(a)(N2-3.4%H2-15.5%H2O(PO2=9.3×10-18atm))及びガス(d)(N2-16.9%O2-15.5%H2O(PO2=1.7×10-1atm))中におけるSUS304鋼の重量変化曲線を示す。いずれも,炉内ガス温度が下がった時に重量減が生じている様子が分かる。特に酸素分圧の高いガス(d)では,温度低下時に毎回重量減が見られた。ガス(a),(d)のいずれも,スケール剥離後の酸化速度が徐々に低下しているのは,図6-14に示したように,酸化スケールが全て剥離するのではなく,部分的に残存するためと考えられる。このように,大気中では良好な耐酸化性を示す条件下であっても,水蒸気含有環境で熱サイクルがかかる場合においては,十分な耐酸化性を示さないことがあるので注意を要する。
図6-16に,水蒸気含有量が一定で酸素分圧が異なる環境におけるSUS304鋼及びSUS310S鋼のスケール厚さを示す。SUS304鋼は,水蒸気含有量が等しい場合,酸素分圧が高い環境ほど酸化スケールも厚くなった。一方,SUS310S鋼は,いずれの酸素分圧下においても酸化スケール厚さはSUS304鋼の1/10以下であり,かつ,酸素分圧の影響は余り見られず,むしろ酸素分圧が高い環境においてスケールが薄くなる傾向が見られた。Crを25 %含むSUS310S鋼では,Crリッチな保護性皮膜形成することによって,本環境中において加速酸化が抑制されているものと推察される。
ガス組成 | PO2(atm)at 800 ℃ | |
(a) | N2-3.4%H2-15.5%H2O | 9.3×10-18 |
(b) | N2-0.02%H2-15.5%H2O | 2.7×10-13 |
(c) | N2-15.5%H2O | 1.2×10-7 |
(d) | N2-16.9%O2-15.5%H2O | 1.7×10-1 |

図6-12 水蒸気酸化試験装置

図6-13 水蒸気酸化試験における熱サイクルパターン

図6-14 大気中及び水蒸気含有環境に暴露したSUS304鋼の断面
(800℃-250℃サイクル,144h)

図6-15 SUS304鋼の重量変化曲線(800 ℃-250 ℃サイクル)

図6-16 SUS304鋼及びSUS310S鋼のスケール厚さに及ぼす
酸素分圧の影響
4-2 水蒸気酸化挙動に及ぼす合金元素の影響
先に示したとおり,Fe-20Ni-25Crを基本組成とするSUS310S鋼は,SUS304鋼と比較して,水蒸気含有環境において優れた耐酸化性を示す。一方,SUS310系実用合金には,Fe,Ni,Cr以外にも種々の合金元素が添加されている。そこで,Fe-20%Ni-25%Crを基本組成として,実用合金に添加されている幾つかの種類の元素を微量添加した際の耐水蒸気酸化性を調べた。
図6-17に,Fe-20%Ni-25%Cr合金にCe,Si,Nb及びMoを添加してアーク溶解にて溶製したモデル合金を水蒸気含有環境にて酸化した際の,各種合金の酸化スケールの断面写真を示す。0.05 %Ce添加は水蒸気酸化成長抑制にはほとんど寄与しておらず,高酸素分圧環境ではむしろ酸化を助長する結果となった。0.5 %のNbあるいはSi添加合金は,特に低酸素分圧環境で酸化スケール成長の抑制効果が見られたが,Si添加合金には,粒界腐食と思われる局部的浸食が見られた。一方,1.5 %のMo添加は,高低いずれの酸素分圧下でも,基本合金と比較して著しいスケール成長抑制効果が見られた。河内ら26)は, Nb,Mo,W及びTaを添加したFe-30%Ni-20%Cr合金を700 ℃の水蒸気雰囲気で酸化し,Feとの金属間化合物を析出するNb,Mo及びWを添加した合金は,内層スケール厚さが低下することを報告している。これは,添加元素とFeとの金属間化合物が析出することで酸化スケール直下の合金中のCr活量が低下し,合金表面に供給されるCrのフラックスが増加するためと考察している。
今回の実験で1.5 %のMo添加がFe-20%Ni-25%Cr合金の水蒸気酸化スケール成長を抑制した理由が,河内らの考察した理由と同様の理由よるかは,添加量を変えた実験や,元素分布分析などの詳細な検討を行っていないため一概には言えないが,Cr,Ni以外の第三の微量添加元素の種類と添加量によって,水蒸気酸化挙動が大きく変化することは示唆される。したがって,水蒸気酸化挙動は,主要元素に加えて微量添加元素の種類及び濃度に留意して,材料選定・材料設計することが重要となると考えられる。

図6-17 Fe-20Ni-25Cr-X合金に生成した水蒸気酸化スケールの断面
(800℃-250℃サイクル,144h)
5.おわりに
本報では,種々の環境・エネルギー関連装置に見られる高温腐食現象として,浸炭・メタルダスティング,窒化及び水蒸気酸化の事例あるいは実験例を紹介した。詳細な検討ができていない内容も含まれているが,これらの現象は,どんな高温装置にも含まれ得るC,N,H2O存在下において,条件が揃うと顕在化する高温腐食問題であることから,環境・エネルギー関連装置を取り扱う際に留意すべき現象として重要である。
本講座では,著者らが入社以来20年間以上にわたって携わってきた高温腐食事例を基に,それに関わる研究開発事例,対策事例の一部を紹介した。高温腐食は,湿食(水溶液腐食)と比較して実産業界においても遭遇する機会は少なく,このことは腐食の学会における発表件数にも表れている。また,湿食以上に,経済成長や世の中の景気に研究開発投資が左右されるところもある。一方で,一歩間違えば大きな事故につながることも多く,対策が確立されていない現象も多い重要な研究分野であると言える。また,高温腐食は,単なる腐食防食技術でなく,金属組織学,拡散,電気化学,熱力学,反応速度論など,材料工学のほとんど全てが詰まった技術分野であるため,学術的な面及びエンジニアリング的な面の両方から重要であると言え,高温腐食の研究者のみならず,研究開発以外に従事する技術者にも大いに役立つ分野である。
本講座で紹介した技術の多くは,著者らが長年にわたって御指導いただいた北海道大学名誉教授 成田敏夫先生との共同研究によるものである。ここに記して謝辞を表したい。
今後,環境・エネルギー関連装置の高齢化が進むと同時に,IoTやAIなどの情報技術の発展によって,装置の延命技術や新プロセスの開発が飛躍的に進むと思われる。その際にも,高温腐食の知識や技術が重要かつ不可欠になってくることは間違いない。本講座が,環境・エネルギー関連装置の健全性・信頼性維持・発展に少しでも貢献できれば幸いである。
参考文献
1) 熱力学データベースMALT for Windows:㈱科学技術社(2004).
2) F. Neumann, B. Peterson: Beitrag zur Mettallurgie der Gasaufkohlung, Harterei-Techn Mitt., 23, p.296 (1968).
3) R. F. Hackman: Basic studies of metal dusting deterioration “metal dusting” in carbonaceous environments at elevated temperature”, Proc. 4th International Congress on Metallic Corrosion, NACE, p.258-263 (1972).
4) H. J. Grabke, R. Krajak, J. C. Nava Paz: On the mechanism of catastrophic carburization: ʻMetal Dusting’, Corrosion Science, 35, p.1141-1150 (1993).
5) H. J. Grabke, R. Krajak, E. M. Miller-Lorenz, S. Strauss: Metal dusting of nickel-base alloys, Materials and Corrosion, 47, p.495-504 (1996).
6) R. Schneider, E. Pippel, J. Woltersdorf, S. Strauss, H. J. Grabke: Micro processes of metal dusting on nickel and nickel-base alloys, Steel Research, 68, p.326-332 (1997).
7) H. J. Grabke: Metal dusting, Materials and Corrosion, 54 (19), p.736-746 (2003).
8) H. Yakuwa and T. Kataoka: Proceedings of Turbo Expo 2007, GT2007-27362, Montreal (2007).
9) G. Y. Lai: High-Temperature Corrosion of Engineering Alloys, ASM Intl, p.37 (1990).
10) 西田恵三,成田敏夫共訳:㈳腐食防食協会偏,“金属の高温酸化入門”,丸善,p.57(1982).
11) ㈳腐食防食協会偏:“金属材料の高温酸化と高温腐食”,丸善,p73(1982).G. C. Wood, I. G. Wright, T. Hodgkies and D. P. Whittle: Materials and Corrosion, A comparison of oxidation of Fe-Cr, Ni-Cr and Co-Cr alloys in oxygen and water vapour, 21, p.900-910, (1970).
12) G. Y. Lai: High-Temperature Corrosion of Engineering Alloys, ASM Intl, p.59 (1990). H. J. Grabke, U. Gravenhorst, W. Steinkusch: Carburization of chromium nickel steels in a carbon bed, Materials and Corrosion, 27 (5), p.291-296 (1976).
13) 例えば,腐食防食協会編:腐食・防食ハンドブック(第2版)CD-ROM編,Ⅱ_8_3_3,(2004).
14) 火力発電技術協会関東支部ボイラチューブ事故調査委員会:ボイラチューブ事故調査報告,火力原子力発電,24(10),1177-1227(1973).
15) 谷村昌幸,中沢利雄:アンモニア合成塔での現用鋼の水素浸食および窒化による腐食脆化について,防食技術,21(5),p.209-218(1971).
16) 大久保勝夫:高圧設備の腐食とその対策,圧力技術,18(1),p.39-46(1980).
17) 田村孝市,中原正大,高橋克:低圧アンモニア雰囲気中での炭素鋼の窒化事例,腐食防食’91講演集,p.57-60(1991).
18) R. G. Rowe, H. Yakuwa, H. H. Vakil, A. Whitehead, M. Miyasaka, and R. Kikuta: Environmental effects on steam turbine structural materials in an NH3/H2O atmosphere, Proc. High-Temperature Corrosion and Protection 2000, p407, Rusutsu (2000).
19) 諸石大司:ボイラ過熱器ステンレス管の水蒸気酸化,防食技術,25(2),p.97-104(1976).
20) S. Jianian, Z. Longjiang, and L. Tiefan: High-temperature oxidation of Fe-Cr alloys in wet oxygen, Oxid. Met.48 (3/4), p.347-356 (1997).
21) C. T. Fujii and R. A. Meussner: Oxide Structures Produced on Iron - Chromium Alloys by a Dissociative Mechanism, J. Electrochem. Soc., 110 (12), p.1195-1204 (1963).
22) C. T. Fujii and R. A. Meussner: The Mechanism of the High - Temperature Oxidation of Iron - Chromium Alloys in Water vapor, J. Electrochem. Soc., 111 (11), p.1215-1221 (1964).
23) A. Rahmel and J. Tobolski: Influence of water vapour and carbon dioxide on the oxidation of iron - silicon alloys in oxygen at temperatures of 750 to 1050 ℃, Mmaterials and Corrosion, vol.16 (8), p.662-676 (1965).
24) A. Yamauchi, K. Kurokawa and H. Takahashi: Evaporation of Cr2O3 in Atmospheres Containing H2O, Oxidation of Metals, 59 (5/6), p.517-527 (2003).
25) K. Nakagawa, Y. Matsunaga and T. Yanagisawa: Corrosion behavior of ferritic steels on the air sides of boiler tubes in a steam/air dual environment, Materials at High Temperatures, Vol.20, p.67-73 (2003).
26) 河内礼文,西山佳孝:析出物形成元素を添加したオーステナイト系ステンレス鋼の耐水蒸気酸化性に関する熱力学的考察,日本金属学会誌,81(9),p.427-434(2017).
エバラ時報のおすすめ記事
エバラ時報に掲載の記事に関する不明点やご相談は、下記窓口よりお問い合わせください。